Size of the Patch
When it comes to the pricing, the size of the patch is one of the most important aspects to consider. Patches that are larger take more time and resources, which results in an increase in their cost. On the other hand, smaller patches have lower costs because they use less material and require less time to produce. The pricing of custom embroidery patches is directly influenced by the link between the size, the amount of time consumed, and the materials used.
Design Complexity
The complexity of the design is a more important factor than the size of the patch in terms of its significance. Designs that are intricate and feature detailed artwork require additional stitches and effort, which ultimately results in an increase in costs. The opposite is true for simple designs of the same size, which are typically more cost-effective due to the fact that they require less time for manufacture and fewer materials. Therefore, the level of complexity of the design is a significant component that plays a role in determining the cost of custom embroidery patches.
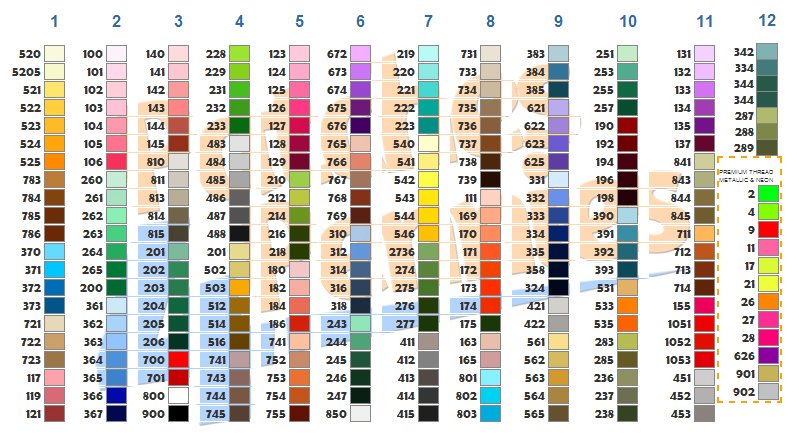
Number of Colors:
The price increases with the number of thread colors used in the design, as each additional color adds to the complexity and production costs. If the number of colors exceeds the number of needles in the machine head, the machine must be stopped to replace the thread, significantly increasing production time. Imagine having to change 5-10 extra colors; this would drastically prolong the production process and further raise the costs.
Embroidered Percentage:
Full embroidery, which covers the entire patch surface, costs more than partial embroidery where some of the base fabric is exposed. For example, customers may choose a black fabric background instead of black embroidery to save on production time and costs. However, patches with 100% embroidery coverage are considered the best and most appealing. They stand out and look high-end compared to patches with 50% or 75% embroidery coverage.
Premium Upgrades:
Patches with special features such as 3D puff embroidery, glow-in-the-dark threads, metallic threads, or unique shapes can increase the cost. The extent to which these premium elements are used will determine the additional expense.
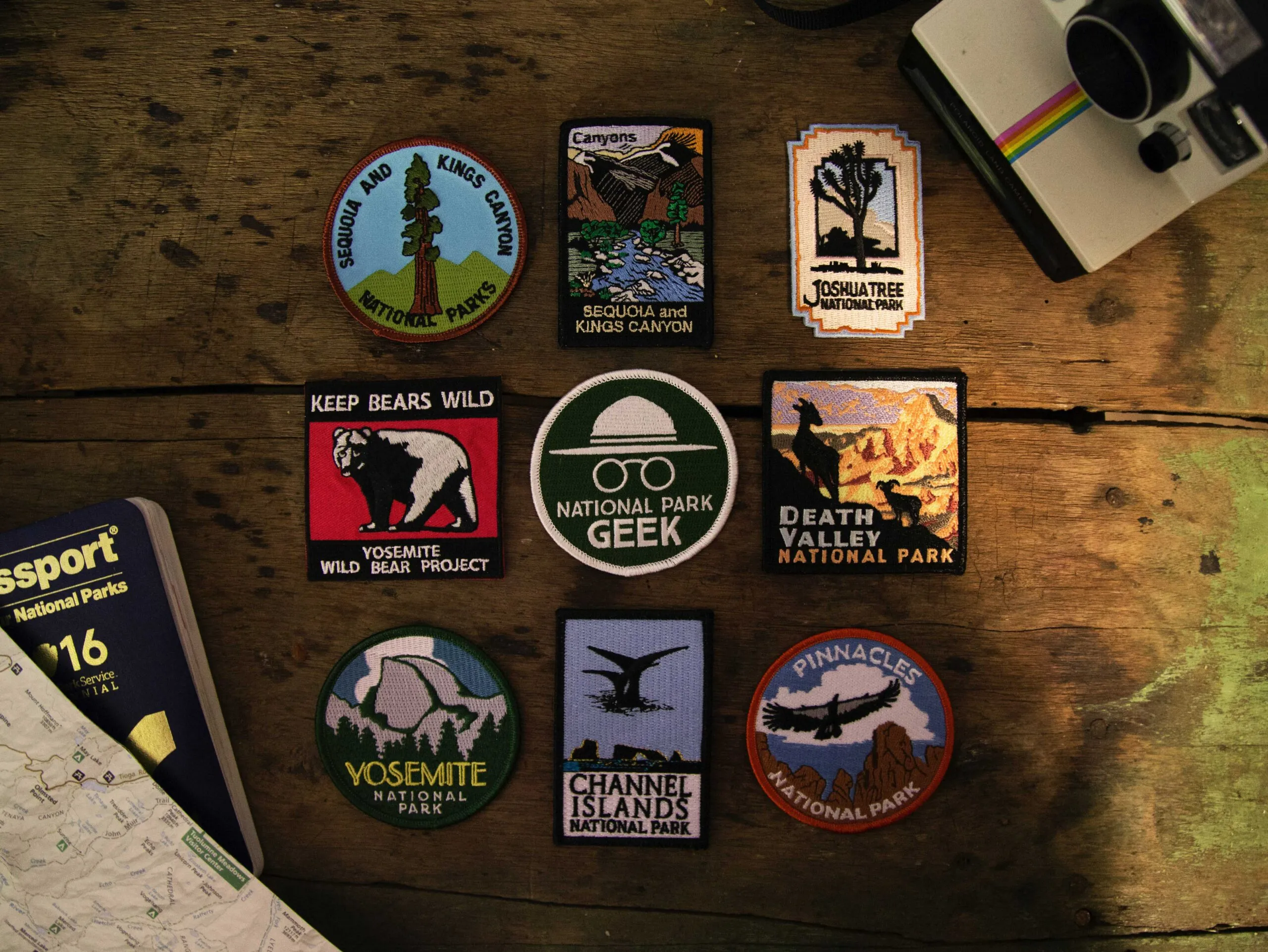
Minimum order Quantity (MOQ)
A minimum order quantity is required for each patch design, and most patch manufacturers have this requirement. When you place an order with Best Custom Patches, we normally demand a minimum purchase of 25 patches; however, there are some instances in which we are willing to accept orders for a single item. Bulk orders typically result in a reduction in the cost per patch, the more the quantity, the cheaper the price per unit. This is because economies of scale and decreased shipping costs apply to larger quantities. It is generally recommended to place an order for at least one hundred pieces to get the best price.
Production Time
When it comes to production time, rush orders demand fast and urgent attention to guarantee seamless production. This may require putting an end to projects that are already in progress. Because of this urgency, the costs are greater in comparison to the usual pricing. Due to the necessity of expedited processing and prioritisation, the actual cost of rush orders is often substantially greater than the cost of regular orders.
When it comes to custom embroidery patches, Best Custom Patches is your go-to choice. Their commitment to quality, design flexibility, and skilled craftsmanship ensures that your patches will stand out. Whether it’s for branding, personal expression, or team spirit, trust Best Custom Patches to turn your vision into a wearable masterpiece!